Deep Hole Drilling Solutions
Star Cutter Express Gundrill Programs

Single Flute Gundrills
The single flute gundrill has the ability to machine straight deep holes and hold excellent finishes. This tool is a general-purpose drill designed for deep hole drilling in virtually any material, can be custom-fit to each application, and is available in a variety of carbide grades & coatings to help optimize tool life and chip evacuation/formation.

Solid Carbide Twist Drills
Solid Carbide Twist Drills are available in custom design and lengths. Geometries vary based on the materials being machined. Tools are designed with polished flutes beyond the cutting area for enhanced chip evacuation. Pilot tools are also available.
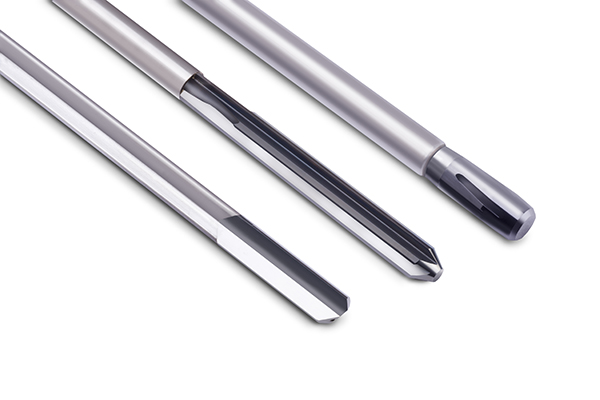
Rifle Buttons / Push & Pull Reamers
Star high precision rifle buttons and push and pull reamers are made to your specific requirements. Products are designed with tight tolerances resulting in improved part quality by achieving controlled size and finishes for a product range of 17-50 caliber.

Two-Flute Two-Hole Gundrills
The two-flute, two-holed “Milled Style Gundrill” is used for high penetration deep hole iron applications, including gray, cast and CGI. The body of this tool is milled out of bar stock which maximizes the rigidity reducing the body deflection at higher RPM.
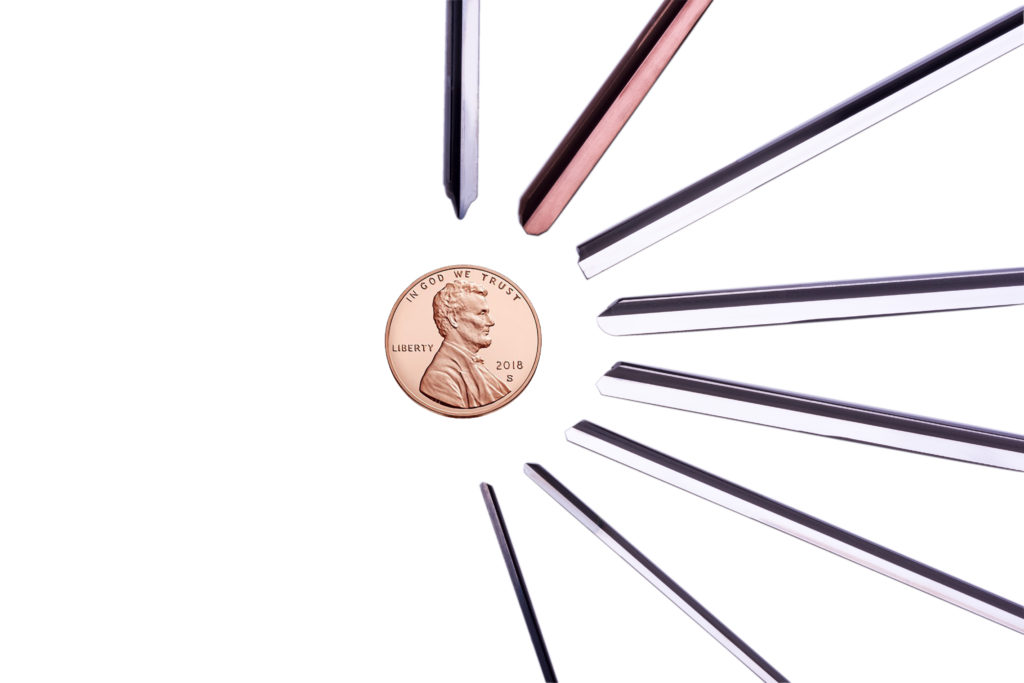
Solid Carbide Single Flute Gundrills
Solid carbide drills are a deep hole drill that can run at much higher feeds rates than conventional gundrills.
These tools can be designed with special end forms to meet your custom requirements. Additionally, special coatings are chosen, based on the application, to enhance overall tool performance.

Double Crimp Gundrills
The term double crimp is derived from the process of crimping the same tube used for the single flute gundrill, only crimping it twice, 180 degrees apart. Therefore, with the flute channels on this type of tool being somewhat shallower then the single flute, they limit the type of materials to be drilled by the chip size generated.

Double Jet Gundrills
Star Cutter, with its years of experience in gundrilling developed a Star original patented Double Jet Gundrill. The most critical interface, in which the carbide is subjected to the most traumas, is during entry/exit of the part and during interruptions of the boring cycle.